Sự khác biệt giữa động cơ servo và động cơ bước
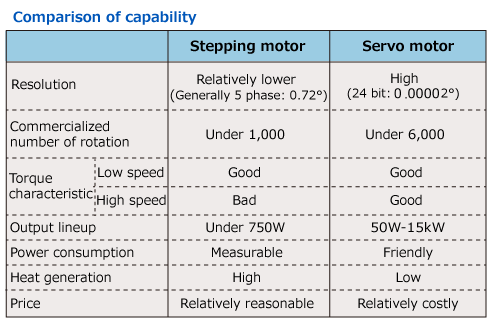
Cả động cơ servo và động cơ bước đều là động cơ đồng bộ có thể điều khiển vị trí. Nhìn chung, động cơ bước thích hợp cho các trường hợp sử dụng tốc độ chậm trong khoảng cách ngắn không đòi hỏi độ chính xác cao trong việc định vị. Mặt khác, động cơ servo góp phần vào các trường hợp sử dụng đòi hỏi độ chính xác định vị cao, di chuyển đường dài hoặc cần tạo ra mô-men xoắn lớn ở tốc độ cao. Tuy nhiên, động cơ servo sẽ có khả năng theo dõi lệnh thấp hơn nếu độ cứng của thiết bị không đủ, trong khi động cơ bước luôn cung cấp hiệu suất theo dõi cao bất kể thiết bị nào. Sau đó, động cơ bước khá rẻ vì cấu trúc đơn giản của chúng, trong khi động cơ servo tương đối đắt vì chúng yêu cầu bộ mã hóa phát hiện vị trí. Tuy nhiên, động cơ servo sẽ góp phần tiết kiệm năng lượng đáng kể nhờ nhiệt lượng mà chúng tạo ra ít hơn, dẫn đến giảm chi phí vận hành.
Sự khác biệt về độ phân giải tùy thuộc vào cơ chế xoay
Với động cơ bước, động cơ có cơ chế vận hành phụ thuộc vào bước góc quay của các răng ăn khớp. Trình điều khiển (bộ khuếch đại) tạo ra các tín hiệu lệnh về phía động cơ dựa trên thời gian của tín hiệu đầu vào của chuỗi xung, như một lệnh định vị trí. Động cơ quay ở các góc bước thiết kế (độ phân giải). Tuy nhiên, độ phân giải bị hạn chế vì nó đòi hỏi độ chính xác gia công cao. Trong trường hợp động cơ servo, động cơ gắn một bộ mã hóa và có cơ chế phản hồi vị trí quay và tốc độ của trục động cơ tới trình điều khiển (bộ khuếch đại). Trình điều khiển (bộ khuếch đại) tính toán độ lệch của các lệnh về vị trí / tốc độ và tín hiệu phản hồi (vị trí / tốc độ hiện tại) từ bộ mã hóa và điều khiển chuyển động quay của động cơ để giữ độ lệch “0”. Động cơ servo nhận ra độ phân giải cao nhờ cơ chế này.
Sự khác biệt về đặc tính mô-men xoắn tùy thuộc vào hệ thống điều khiển
Stepping motors do not have a position detection sensor such as an encoder, instead they control the operation between the driver (amplifier) and the motor with the open-loop system. Therefore, it could cause motor step-out when the allowable torque or more is applied to the shaft from the outside. On the other hand, servo motors always have feedback of position information from the encoder between the driver (amplifier) and the motor, and control the operation with the closed-loop system. Therefore, they are able to correct a temporary positioning fluctuation due to the external force exceeding the allowance and check the status with such as the completion signals of positioning. In addition, servo motors are able to generate the same level of torque both in low-speed region and in high-speed region. Although stepping motors generate high torque in low-speed region, it lowers torque when the speed gets higher.
Difference in electricity consumption and heat generation depending on the structures
Stepping motors keep the flow of electric current through motors at a certain level when they are either operating or stopped. And the loss would increase depending on motor’s rotating speed, so that it increases both electricity consumption and heat generation for that. On the other hand, servo motors require electric current only corresponding to the deviation, it is able to lower electricity consumption and suppress motor’s heat generation as it needs small amount of electric current when the motor stops or is operating at a constant speed.
What is the difference between AC drives and the servos?
Both AC drives and servos are equipment to control motors. Both have the same basic function that rotates motors at an expected speed by converting power from commercial power sources, controlling voltage (current) and frequency. Customers will choose either one of these depending on the performance and the function they need. AC drives have a perfect command of the motor’s rotation speed and supply stable power. And they are constantly advancing by implementing functions which were used to be controlled by host controller as the standard. In addition, 1000 Series AC drives realize controls on various types of motors. They are able to control not only general induction motors but also efficient synchronous motors (with/without PG). There is a wide range of usage for AC drives from living-related devices and social infrastructure facilities that are close to our daily lives to industrial equipment. Moreover, they also contribute to saving energy for the use of fans and pumps by adjusting motor’s rotation speed and suppressing the waste of the electricity consumption.
On the other hand, servos control motors so as to follow-up toward commands of position and speed quickly. The motor controls the dedicated synchronous motor which comes with the encoder. Servos demonstrate a great performance on moving surely and faithfully to the commands of position and speed, so that equipment such as machine tools and semiconductor manufacturing equipment, which requires high-speed and high-accuracy positioning, applies servos.
What is the difference between induction motors and synchronous motors?
A Motor is an electric device which converts electrical energy into mechanical energy. Let’s see the differences between induction motors and synchronous motors from the perspective of the difference of rotation principles, in terms of motor that rotates in rotating magnetic field generated by AC source.
In the case of induction motors, when you insert rotor formed by the metallic coil in the rotating magnetic field, induction current starts to flow through the coil, then the magnetic field generated by this induction current starts to rotate drawn by the magnetic field. The magnetic field of the induction motor generates the rotating magnetic field which has the same cycle of the frequency as the power source. When the rotor rotates drawn by the magnetic field, in fact a slight delay (slip) occurs.
In the case of synchronous motors, when you insert rotor attached with permanent magnets in the same rotating magnetic field as induction motors, the permanent magnets will be drawn to the rotating magnetic field and start to rotate synchronizing to the speed of the rotating magnetic field. Induction motors are hard to break and durable to a harsh environment such as the heat, vibration and impact. It is easy to adjust the scale to a large one as it has a wide capacity range.
Synchronous motors realize a high efficiency of machine with its little motor loss. They are suitable for machine which requires high precision since it is also flexible to the environment change such as temperature. Moreover, it will meet the increasing needs of downsizing and weight reduction since it is relatively smaller than the induction motor. Synchronous motors have two different types of motors further depending on how you assemble permanent magnets to the rotor: SPM (Surface Permanent Magnet) motor and IPM (Interior Permanent Magnet) motor. SPM motors are smaller than IPM motors, however, IPM motors are suitable for high speed rotation.
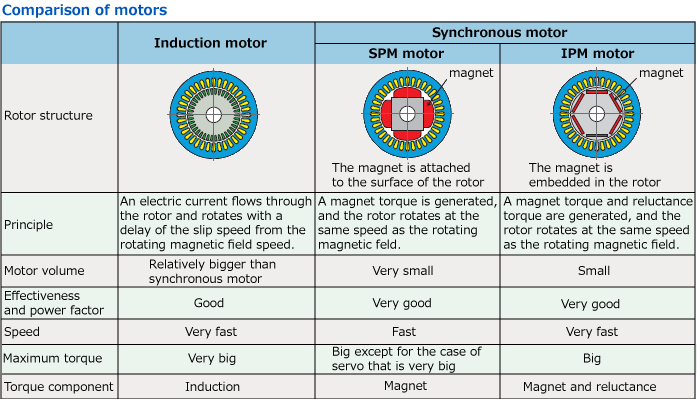
Difference between machine controller and PLC
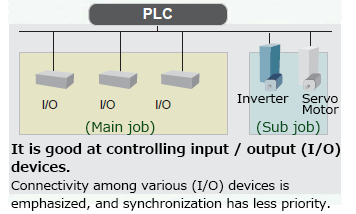
Machine controller and PLC (Programmable Logic Controller) are both controlling devices for machines. PLC has been generated for the purpose of replacing the electromagnetic relay, used in the conventional automation system and executes control based on the preset order. This is called “sequence control”.
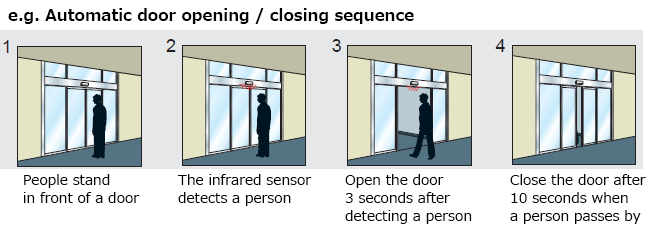
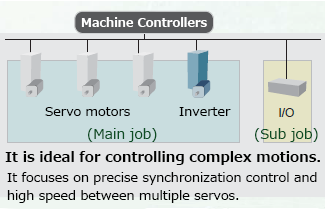
Meanwhile, various machines have been required to offer a higher technical advantages in recent years. Then, a machine controller was generated to control various devices that perform complex motions at high speed using servo and AC Drives. In this background, machine controller and PLC have different purposes, so they are good at different jobs. Machine controllers are good at controlling complex motions at high speed and with high precision, whereas PLCs are good at input / output (I/O) control.
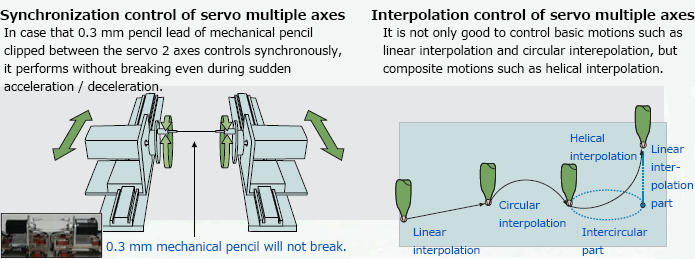
What is an encoder?
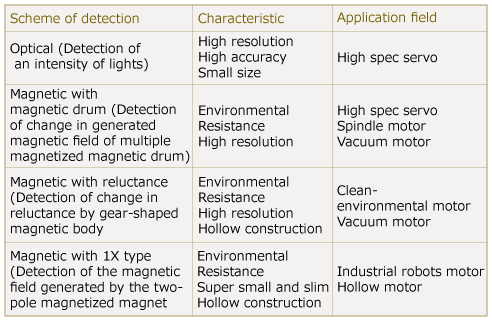
For servo drives, a position sensor (encoder) is essential in order to control the movement (motion control) of the machine/equipment precisely. The performance of the encoder is an important element that influences on not only the control performance of the servo motor but also the performance of the machine/equipment. The encoder requires to be downsized since it will be a part of the machine/equipment combined with servo motors, moreover, it must be durable to the vibration/impact and temperature change in as it should work in a harsh environment. To categorize encoders which Yaskawa has developed by the detection methods, there are a few types of them: Optical encoders and magnetic encoders (magnetic drum, reluctance and 1x type).
Optical encoders
Optical encoders realize high resolution and precision easily and are suitable for high performance rotation servo. They read light receiving elements from the light emitting diode (LED) through the slit set on the rotating disc by the phototransistor and detect the rotation angle by processing the signal.
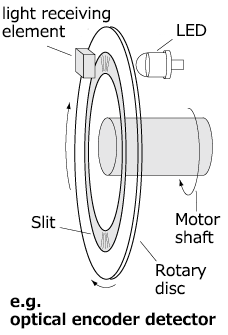
It is possible to improve resolution by increasing the number of slits, instead it makes the diameter of rotating disc larger. When they transmit the position information by pulse output, it would limit the speed of the circuit or the pulse transmission at the high-speed rotation.
Then, by introducing serial transmission which outputs the position information as data and performing multiplying process and transmission format conversion with dedicated ASIC, it realized high resolution and downsizing without increasing the number of slits. Optical encoders have two methods to detect position: the incremental method which sets a base point when the power is on, and the absolute method which possesses the displacement information from the origin regardless of the on/off of the power and retrieve this information when the power is on. Through developing dedicated ASIC with improved processing speed, Yaskawa has developed both incremental and absolute encoders with 20bits resolution (approximately 1million pulses/rotation) and improved the performance of servo drives.
Magnetic encoders
Magnetic encoders have excellent environment resistance. Among magnetic encoders, both magnetic drum and reluctance types are able to enhance resolution, so that motors such as spindle motor for machine tools and vacuum motors introduce them. Meanwhile, 1X types are excellent in downsizing, flexibility to high-speed rotation and hollow structure, therefore they are applied to micro servo motors, hollow motors for robots and others. Let’s see what is the 1X type suitable for downsizing.
1X type magnetic encoders
They use the mechanism that a signal, which detect the magnetic field generated by the magnets magnetized to two poles by magnetic field sensor, makes one cycle of sine wave with a single rotation (1X: The structure generates one cycle of signal with a single rotation). One pair of the magnetic field sensor (+A and -A, +B and -B) generates analog signals of one cycle of sine wave or cosine wave in a single rotation of the magnet. By calculating the arc tangle of these signals, it returns the rotation angle (the absolute position within one rotation). The 1X type magnetic encoder is set to detect the continuous magnetic field, so that the precision of the output signal and the resolution of the encoder are possible to enhance even with a small sized one as they are dependent on the precision of magnetic field detection and signal processing. Its signal processing part can be separated without installing in the motor, the encoder has excellent vibration resistance. The encoder is also flexible to high-speed rotation and hollow structure.
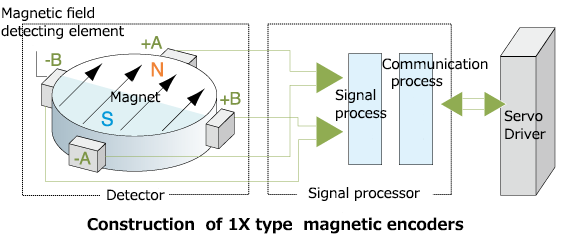